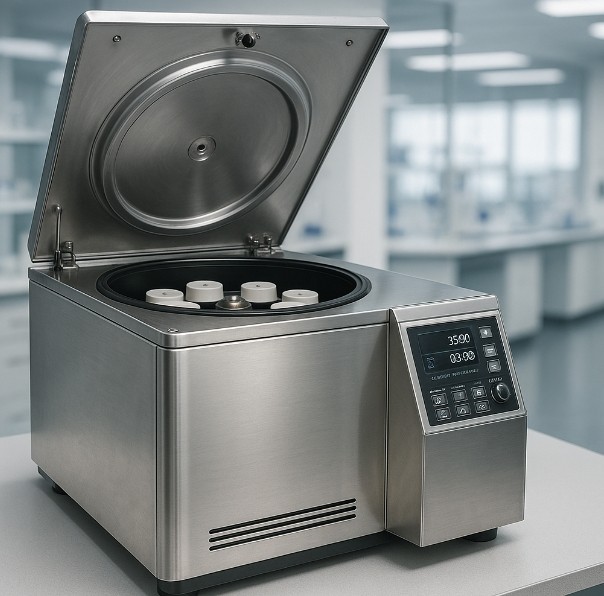
管架离心机如何确保转子在高速状态下不松动?
一、引言
管架离心机在生物、化工、临床等领域广泛应用,其高速旋转所产生的巨大离心力对转子紧固提出极高要求。一旦转子松动,不仅会导致分离效率下降,还可能造成设备损坏、样品泄漏甚至人员伤害。本文将从设计选型、安装操作、日常维护、监测校验及应急预案等方面,系统阐述如何确保管架离心机转子在高速状态下始终保持紧固、稳定与安全。
二、设计选型层面
转子与轴承配合公差控制
选用符合 ISO 8662 或 GB/T 9472 等标准的高精度转子,轴孔与主轴配合过盈量在 0.01–0.03 mm 之间,保证装配时产生可靠的摩擦锁紧作用。
采用渐开线锥形配合或椎销定位设计,利用锥度配合增大接触面,避免侧向滑移。
高级紧固件与锁紧机构
配备专用高强度螺母与弹性垫圈,弹性垫圈在扭矩作用下持续施加预紧力;
设计机械锁片或安全线销,防止螺母自转松脱;某些机型还采用多级锁紧结构,在主锁紧件之外增设辅助锁定件。
预紧力监测与报警
内置力传感垫或应变片,实时测量螺栓预紧力;
当预紧力低于设定阈值(如扭矩值的80%)时,自动发出声光报警并禁止继续加速。
三、安装操作规范
清洁与润滑
安装前必须清除主轴及转子内孔上的油污、尘埃和腐蚀产物;
对配合面涂抹适量专用抗咬合润滑剂,既保证摩擦锁紧,又防止金属冷焊。
扭矩控制拧紧
使用校准过的扭矩扳手,按照设备说明书推荐值(例如 50 N·m ± 5%)均匀紧固;
扭矩扳手应定期校验,确保读数准确性。
逐步过渡启动
初次加速至30%额定转速后暂停 10–15 s,检查振动和预紧状态;
若无异常,再分段加速到目标速度,避免一次性大扭矩冲击导致松动。
四、日常维护与检查
定期拧紧检测
每使用 100 h 或每月一次,用扭矩扳手校验并必要时重新拧紧主螺母;
维护日志记录每次检测结果与实际扭矩,形成可追溯档案。
振动与温度监控
在腔体外壳安装三轴加速度传感器,监测震动趋势;
在主轴轴承座部位设置温度传感器,温度急升往往预示润滑失效或预紧力下降。
动平衡校验
每季度使用在线动平衡系统,自动收集不平衡幅值与相位,及时调整转子配对和重量分布;
平衡不良时禁止高转速运行,并在平衡台上进行重新校正。
五、生产与质量控制
转子制造工艺
采用高精度 CNC 铣削与磨削,加工偏差严格控制在 0.005 mm 以内;
表面热处理和硬度控制,减少转子孔径与轴承座的磨损。
入厂检验与出厂检测
出厂前所有转子必须通过超声探伤检测和涡流裂纹检测,确保无微裂纹;
经过加速寿命试验(如 10 000 h 连续模拟运行),并对紧固件循环拧紧试验不少于 1 000 次。
六、操作培训与管理
标准操作程序(SOP)
制定详细的转子安装、拧紧、启动及停机步骤;
明确操作人员资质要求,未经培训不得擅自操作或维护。
技能考核与复训
每半年对应急拆装、拧紧检测与振动监测进行考核;
对新技术(如在线监测、远程诊断)定期开展培训,保持操作水平与设备性能同步提升。
七、应急预案与故障处理
松动预警响应
振动超标或扭矩过低报警时,立即切换至缓速制动模式,并停止进一步加速;
开启后台远程诊断,指导现场人员进行可视化检查。
手动紧急停机
若转子出现剧烈异响或突然失衡,操作人员可按下“紧急锁紧”按钮,在离心机继续转动但锁定螺母的状态下平稳停机,避免螺母甩出。
故障部件隔离
发现螺纹滑丝或转子孔损伤时,立即停机隔离,禁止继续使用;
损坏部件需送回生产厂商进行检修或更换,并对同批次产品开展回溯检测。
八、前沿技术与未来趋势
智能紧固系统
采用电磁锁或气动锁紧机构,实现无接触紧固与自动加锁;
结合机器学习算法,基于运行数据预测预紧力下降趋势并自动补偿。
无线监测与大数据分析
通过无线传感器网络将转子振动、温度与扭矩数据实时上传云端;
利用大数据分析和故障诊断模型,提前预警并优化维护计划。
新型材料与自润滑合金
开发低摩擦、高强度的钛合金或陶瓷涂层转子,减少对螺母预紧力的依赖;
应用自润滑材料,降低因频繁拧紧造成的磨损与预紧力衰减。
九、结语
确保管架离心机转子在高速状态下不松动,需要从设计、制造、安装、监测到管理的全生命周期加以控制。通过高精度配合、专用紧固件、严格的安装与检测流程,以及在线监测与智能预警技术,能够最大限度地降低松动风险,提升设备可靠性和实验安全性。面对实验室多样化需求与运行环境挑战,持续优化技术和管理,将是保障离心分离工作长期稳定、高效运行的关键。