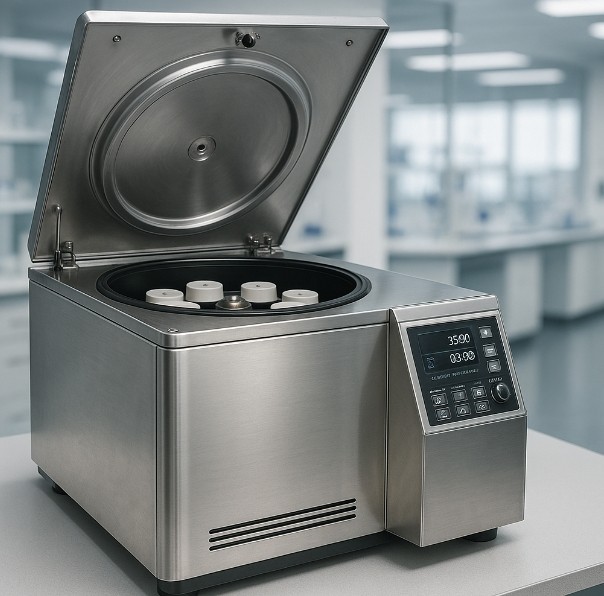
管架离心机转子结构对离心效果有何影响?
一、引言
管架离心机的核心部件为转子,其结构形式直接决定着离心机的分离性能、处理能力和稳定性。不同转子结构在离心力分布、流体动力学特性、机械刚度及热力学行为上各有差异,从而对固液分离效率、沉降速度、样品剪切伤害以及能耗水平产生显著影响。深入理解转子结构与离心效果之间的内在关联,是提升设备性能、优化工艺参数、保证稳定运行的基础。
二、转子结构的主要类型
桶式转子(Basket Rotor)
特点:容积大、散热快,适合高含固量物料;
应用:污泥脱水、果蔬渣液分离、发酵菌体回收。
盘式转子(Disc Stack Rotor)
特点:由多片薄板叠加形成狭缝,离心面积极大;
应用:澄清度要求高的液液分离,如油水分离、乳化液破乳。
筒式-篮筐复合转子(Cylindrical–Basket Hybrid)
特点:集固液分离与浓缩功能于一体;
应用:高粘度或纤维状物料,既需澄清上清又需浓缩沉渣。
锥形分液转子(Conical Rotor)
特点:锥形结构利于沉渣排出;
应用:结晶工艺中晶体快速分离。
可调间隙转子(Adjustable-Gap Rotor)
特点:可根据物料特性调节板间距或筒壁间隙;
应用:多品种生产线,需求灵活切换不同尺寸颗粒分离。
三、关键结构参数及其作用
1. 离心半径(r)
定义:转子内壁到轴心的距离;
影响:离心力F=mω²r,r越大产生的离心加速度越高,可缩短沉降时间、提高分离效率;但增大半径也意味着更大的机械应力和惯性负载。
2. 离心面积(A)
定义:物料在转子内可被离心分离的有效表面积;
影响:A与沉降面积正相关,面积越大,单位时间内通过的物料越多,换言之处理量更大;同时也意味着更大流速,需考虑剪切力与湍流。
3. 板片角度与间距(α、δ)
板片倾角(α):决定流体沿板片的流动方向与沉渣滑脱方向;
板隙宽度(δ):可调节颗粒分离临界粒径,小间距可截留更细微颗粒,但易堵塞;
优化原则:倾角一般取50°~70°,保证固体能顺利滑落;板隙大小根据物料粒度分布确定,可采用实验优化。
4. 结构刚度与振动特性
材料与壁厚:高强度合金或复合材料可在保证刚度的同时减轻重量;
动平衡等级:符合ISO G2.5及工况要求,低振动有利于长期稳定运行;
影响:刚度不足或动平衡差会导致不平衡振动,降低分离效果并危及安全。
5. 热力学与散热性能
摩擦与流体阻力产生热量:连续运行时转子表面与物料摩擦及内部摩擦会产生热;
散热设计:通孔、肋带与散热槽可加速热量散发,避免局部过热导致物料变性或粘附;
影响:温升过高会改变液体粘度及密度,进而影响沉降速率及分离界面稳定性。
四、转子结构对分离效率的具体影响
1. 分离因子(Σ)
定义:等效沉降面积与转速平方之乘积的积分,用于衡量沉降效率;
转子影响:不同结构的Σ值相差可达数量级,典型盘式转子Σ高,可对细微颗粒进行高效澄清;桶式Σ较低,但适合高浓度大粒径沉降。
2. 药剂使用与处理能力
药剂添加:在给定转子结构下,药剂(如混凝剂、絮凝剂)的投加可显著提升效率,但对板式结构敏感度更高;
通过量:盘式可达到数百升/小时,大容量桶式通常限于几十升/小时;混合式则介于两者之间。
3. 脱水与浓缩性能
残渣含水率:盘式转子因板缝排水快,可获得低含水率沉渣;桶式因滤布或内衬影响,含水率较高;
浓缩比:锥形与混合式转子常用于高浓缩场合,可达到30%~50%含固率。
五、流体动力学与剪切力分析
切向速度分布
转子根部与外沿切向线速度不同,流体在转子内部呈径向向外运动,速度梯度产生剪切;雷诺数与流动状态
高转速下流动多为湍流状态,湍流使固体悬浮并重新被搅动,不利于沉降;应通过结构设计降低局部湍流。边界层厚度
边界层过厚会阻碍颗粒跨越层流区域沉降;合理的板片间隙与锥度设计可减薄边界层。
六、转子材料与表面处理
材料选型:316L不锈钢、双相钢、钛合金或哈氏合金,主要依据物料腐蚀性与机械应力;
表面处理:电抛光、喷砂、氟碳涂层或聚四氟内衬,以降低表面粗糙度、防止物料粘附、提升清洗效率;
影响:表面粗糙度越低,分离界面越稳定;涂层与内衬则可扩展耐腐蚀耐磨性,适应复杂工艺需求。
七、转子结构优化设计策略
数值模拟:运用CFD结合有限元分析,模拟流场分布、剪切力及温升效果,指导板片角度、板隙和散热孔位置优化;
模块化可替换设计:开发可拆卸换型模块,如不同缝隙规格的板堆,满足多工艺切换需求;
轻量化与高强度相结合:选用高性能合金或复合材料,减轻转子惯量,提升响应速度与启动可靠性;
动平衡与振动监测集成:在制造与校验过程中引入在线振动监测,保证出厂及现场安装后的平衡等级;
表面微观结构优化:通过激光或化学蚀刻技术,构建微流道或微凹凸面,增强沉渣自动滑移与排渣效率。
八、应用案例
案例一:啤酒酵母回收
某啤酒厂引入板式转子,将板隙由0.1毫米调至0.05毫米,并通过CFD优化板片倾角,结果回收酵母浓度由6%提升至12%,处理量增加30%,清澈度保持不变。
案例二:造纸废水固液分离
使用桶式转子增加内网孔密度,并在外筒加设螺旋导流槽,改进后滤液浊度下降50%,泥饼含水率从75%降至65%,能耗降低15%。
九、结语
管架离心机转子结构在设计上涉及几何参数、材料强度、流体动力与热力学等多重因素,其优化不仅能显著提升分离效率和处理量,还能降低能耗、减少物料损失并延长设备寿命。通过理论分析、数值模拟与现场试验相结合的方式,不断探索创新结构与材料组合,方能在不同工况下实现优异的离心效果。未来,随着智能制造与新材料技术的发展,转子结构设计将向更高的精准化、模块化与数字化方向演进,为分离工程领域提供更强大的技术支撑。