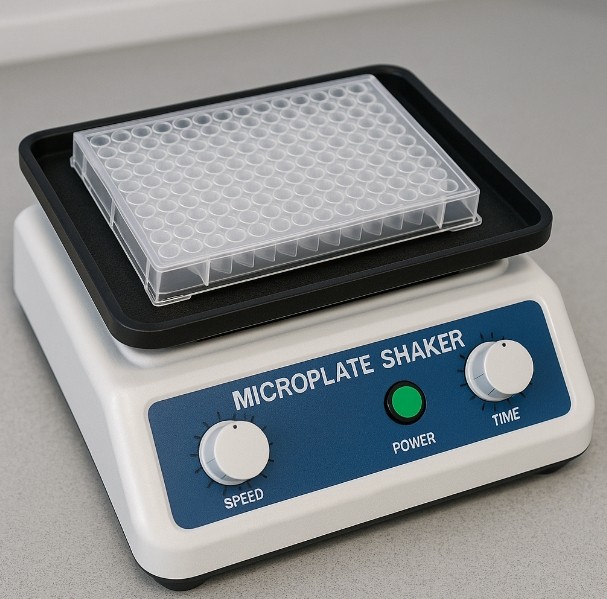
微孔板振荡器节能降耗设计?
微孔板振荡器节能降耗设计研究
一、引言
随着生命科学、高通量筛选、细胞培养等领域对微孔板振荡器的依赖日益增强,其能耗水平亦随之上升。若能在振荡器设计中引入节能降耗技术,不仅可降低设备运行成本,也可减少实验室碳足迹,推动绿色实验室建设。本文从电机选型、驱动控制、机械结构、热管理与系统集成等方面系统探讨微孔板振荡器节能降耗设计方案,以期为相关产品与科研提供参考。
二、电机与驱动系统的优化
高效无刷直流电机(BLDC)应用
无刷直流电机相比传统有刷电机具有更高效率(可达85%以上)、寿命更长、维护需求低等优点。
采用永磁材料优化定子和转子结构,在相同体积下提升功率密度。
智能化驱动控制器
引入基于DSP或MCU的矢量控制算法,通过实时测量电流、电压及转速信息,实现高精度磁场定向控制,降低空载及部分负载时的能耗。
在不同振荡模式下(恒速、脉冲、梯度)自适应调整PWM占空比与电流限幅,确保能效最优。
再生制动与能量回收
在振荡停止或速度切换过程中,利用再生制动技术将电机制动能量回馈至蓄电池或直流母线,减少浪费。
考虑应用小容量超级电容器,平滑瞬态能量回收与释放。
三、机械结构与传动系统节能设计
轻质高强度材料选用
平台与振荡机构采用铝合金或玻璃纤维增强复合材料,减轻惯性负载,降低启动、加速过程中的功率需求。
通过有限元分析优化结构厚度与肋状支撑布局,兼顾强度刚度与减重。
低摩擦滚动支撑与线性导轨
在振荡副、联轴器以及滑动接触面处,采用高精度滚珠轴承与低摩擦系数的特氟龙涂层衬套,减少摩擦损失。
对于直线运动振荡平台,优选滚柱导轨或循环滚珠导轨,提升运动平稳度并降低驱动扭矩。
弹性联轴与动力均衡
在电机与振荡平台之间布置弹性联轴器,可在不对称载荷或细微偏心时吸收振动,减少额外功率消耗。
精确匹配电机、减速器及振荡平台的惯量比,实现在不同负载工况下的最佳能量传递。
四、温度与热管理优化
温控风扇与被动散热结合
电机与驱动板工作时会产生热量,宜选用静音、调速型小型离心风扇,根据温度传感器数据动态调节风量,避免全速运行带来的额外功耗。
机箱内部采用开槽散热片和导热硅脂,将热量均匀引导至外壳后侧自然对流散热。
热绝缘与保温设计
在需要维持温度敏感实验环境中,振荡器底座及侧壁可采用轻质隔热材料,降低外界热交换。
对于带加热或制冷功能的复合振荡器,内置高效隔热层减少能量损失。
智能温度补偿控制
结合实验室环境温度、振荡板承载温度,自动调整风扇与加热/制冷模块的运行时序,避免持续满负荷运行。
五、控制算法与用户界面节能策略
基于模型的预估控制(MPC)
利用振荡平台的动力学模型,对未来一段时间的负载变化进行预测,通过优化算法提前调整驱动信号,实现能效最优。
工况自适应与节能模式
提供“节能模式”与“高速模式”切换选项。在低速或短程振荡时自动切换至能耗更低的控制参数。
在程序编辑界面中,用户可设定时间段、振幅、频率等工况组合,并由系统评估能效,实现一键启动最优节能流程。
远程监测与智能调度
将振荡器接入实验室物联网(IoT)平台,实时采集功耗数据、使用时长与故障信息,结合云端大数据分析,为调度运行时间和维护周期提供决策支持。
通过手机App或Web端,管理员可远程关闭闲置设备,或根据实验需求批量集中调度运行,杜绝无效空转。
六、辅助节能措施与可持续发展
可替换模块化设计
模块化电机、驱动板与振荡平台接口统一,便于后期升级或更换更高效组件,延长整体设备使用周期。
低功耗待机与自动休眠
在连续无操作超过设定时长(如5分钟)后,自动进入低功耗待机状态,仅保留通信与监测功能,待接收到启动指令或定时唤醒时再恢复全功耗运行。
绿色材料与可回收包装
在机壳、支架等零部件的材料选型上,优先考虑可再生或易回收利用的塑料与金属;包装采用瓦楞纸、玉米淀粉基泡沫等可降解材料,减少物流环节中的碳排放。
七、案例分析
某实验室在升级其老旧微孔板振荡器时,按上述设计思路:
将旧有有刷电机替换为BLDC电机,效率提升20%。
增加闭环矢量控制器及能量回收模块,降低峰值功耗30%。
优化平台材料及滚珠导轨结构,使惯性负载减少15%,并将待机功耗由2 W降至0.2 W。
总体年运行成本降低约25%,实验室碳排放量减少近1.2 吨。
八、结论与展望
微孔板振荡器的节能降耗设计需从电机驱动、机械结构、热管理、控制算法及系统集成等多维度协同优化。未来,随着人工智能与物联网技术的发展,可进一步引入深度学习算法进行更精准的能耗预测与控制;同时,新型磁悬浮支撑、声波驱动等前沿技术也将为振荡器的无摩擦低耗运行带来更多可能。通过持续迭代与实践,微孔板振荡器能效水平将迈向更高台阶,助力绿色实验室与可持续科研的实现。