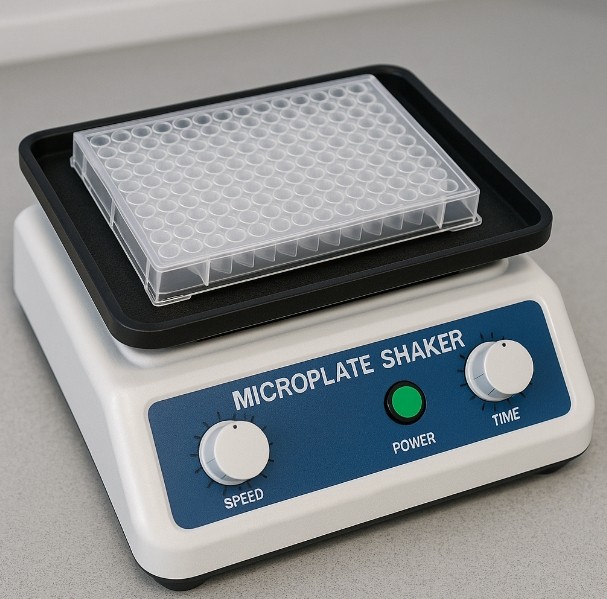
微孔板振荡器电机线圈温度监测?
随着自动化与智能化技术的不断进步,微孔板振荡器电机温度监测已逐渐从传统的定期人工检测向在线实时监控发展。本文围绕电机线圈温度监测的技术方法、数据处理、故障预警及应用实践展开系统阐述,旨在为相关领域的工程技术人员和研究者提供参考。
微孔板振荡器电机线圈温度监测技术研究
一、引言
微孔板振荡器作为实验室中不可或缺的设备,其电机是关键驱动部件。电机在运行过程中,线圈温度的变化直接影响设备性能与使用寿命。过高的线圈温度会加速电机绝缘材料的老化,甚至导致烧毁,造成设备故障和实验中断。因而,实时监测电机线圈温度成为保障设备安全运行和延长寿命的重要手段。
随着自动化与智能化技术的不断进步,微孔板振荡器电机温度监测已逐渐从传统的定期人工检测向在线实时监控发展。本文围绕电机线圈温度监测的技术方法、数据处理、故障预警及应用实践展开系统阐述,旨在为相关领域的工程技术人员和研究者提供参考。
二、电机线圈温度监测的重要性
2.1 电机线圈温度的影响机理
微孔板振荡器电机主要由定子线圈和转子构成。定子线圈通电后产生磁场,驱动转子旋转。在线圈内部,由于电阻存在,电流通过时产生焦耳热,导致线圈温度上升。温度升高会影响以下方面:
绝缘材料老化:高温加速绝缘漆和线圈包裹材料的化学劣化,降低绝缘强度,增加短路风险;
电阻变化:温度变化引起线圈电阻变化,影响电机性能及效率;
机械应力:热胀冷缩产生机械应力,可能导致线圈脱落或断裂;
设备安全隐患:过热可能引发火灾或电机损坏。
因此,监测线圈温度有助于及时发现异常状况,采取保护措施,避免严重后果。
2.2 微孔板振荡器电机温度监测的特殊性
微孔板振荡器通常体积较小,运行环境复杂多变,温度监测面临以下挑战:
空间限制:电机内部结构紧凑,布设温度传感器受限;
动态负载变化:实验样品重量及振荡频率不同导致负载变化,温度波动明显;
环境干扰:振动、湿度和电磁干扰影响测量精度;
维护难度:设备需保持清洁和无菌,传感器安装不能影响实验环境。
因此,选择合适的温度监测技术与传感器类型尤为关键。
三、电机线圈温度监测技术
3.1 直接测温技术
直接测温指将温度传感器直接安装在线圈附近或包裹线上,以获得精准的线圈温度数据。常用传感器包括:
热电偶:利用两种不同金属接触点产生的热电势变化测温。优点是响应速度快,耐高温,缺点是体积较大,安装复杂,且易受振动影响。
热敏电阻(RTD):基于金属电阻随温度变化原理,具有高精度和稳定性,适合中低温区监测。但线圈缠绕区域有限,布置复杂。
热敏电阻(NTC/PTC):热敏电阻成本低,体积小,但精度略低,适用于辅助监测。
光纤温度传感器:利用光纤布拉格光栅技术,可嵌入线圈绝缘层,实现非电气测温,抗电磁干扰强,适合高精度场合。
直接测温的最大优势是温度数据真实反映线圈局部温度,但缺点是传感器布置和维护难度较大。
3.2 间接测温技术
由于直接测温难度较大,间接测温方法通过测量电机其他部位的温度或电气参数,推算线圈温度。
定子壳体温度测量:在电机外壳表面安装温度传感器,结合热传导模型估算线圈温度。优点安装方便,缺点是响应滞后且受环境影响大。
电机参数法:基于电机电流、电压和功率损耗等参数,利用数学模型计算线圈发热量,间接推算温度。
热模型仿真:构建电机热传导数值模型,结合实时传感器数据,实现温度预测。
间接方法灵活便捷,适合现有设备改造,但准确度较低。
3.3 无线与智能传感技术
为提高监测的便利性与实时性,现代微孔板振荡器温度监测采用无线传感器网络和智能算法:
此类技术促进了微孔板振荡器智能化管理。
四、温度数据处理与故障预警
4.1 数据预处理
采集的温度数据通常含有噪声和异常点,需要进行滤波和校正。常用方法有:
滑动平均滤波:平滑短时波动;
卡尔曼滤波:结合模型动态调整估计值;
异常检测算法:剔除突发异常点。
高质量数据是后续分析的基础。
4.2 温度趋势分析与特征提取
通过分析温度曲线的变化趋势,提取关键特征:
最大温度峰值及出现时间;
温度上升速率;
日夜温度波动幅度;
长期累积温升。
这些特征有助于识别设备运行状态和退化趋势。
4.3 故障诊断与预警模型
结合温度特征和历史数据,建立故障诊断和预警模型:
阈值预警法:设定温度上限阈值,超限触发报警;
趋势预测法:利用时间序列模型预测未来温度,提前预警;
机器学习方法:采用支持向量机、随机森林等分类算法,根据多维特征判断故障概率;
深度学习:基于LSTM等网络进行状态识别和剩余寿命估计。
多层次预警策略提升了监测系统的智能化水平和准确率。
五、实际应用案例分析
某生物实验室部署微孔板振荡器电机线圈温度在线监测系统,具体做法如下:
选用光纤布拉格光栅温度传感器嵌入线圈绝缘层,实现精准实时测温;
采集电机运行电流、电压及环境温度数据,构建综合监测平台;
利用卡尔曼滤波处理温度数据,剔除环境噪声影响;
基于支持向量机算法实现故障预警,结合设备维护日志不断优化模型。
部署后,该系统成功识别出2起潜在过热隐患,提前通知维护团队,避免了设备损坏,保障了实验连续性。
六、未来发展趋势
随着智能制造和物联网技术的推进,微孔板振荡器电机温度监测将呈现以下发展方向:
多传感器融合监测:结合温度、振动、电流等多维度数据,构建更全面的设备健康画像;
边缘计算与云平台结合:实现本地快速处理与远程大数据分析的协同,提高响应速度和预测准确率;
自适应智能预警:通过在线学习机制,自动调整预警阈值,适应设备运行环境变化;
微型化与无损检测技术:开发更小型、灵敏度更高的传感器,降低安装难度,保证设备完整性;
数字孪生技术应用:构建电机数字孪生模型,实现虚拟仿真与现实监测的无缝融合。
这些技术将极大提升微孔板振荡器电机的安全保障水平和运维效率。
七、总结
微孔板振荡器电机线圈温度监测是保障设备安全、高效运行的重要环节。本文系统介绍了电机线圈温度的影响机制,重点分析了直接与间接测温技术,结合现代智能传感和数据分析方法,提出了多层次的温度监测与预警策略。通过实际案例验证,所述方法能够有效提升设备的故障预防能力。未来,随着技术的发展,微孔板振荡器电机温度监测将更加智能化、集成化,为实验室自动化提供坚实保障。