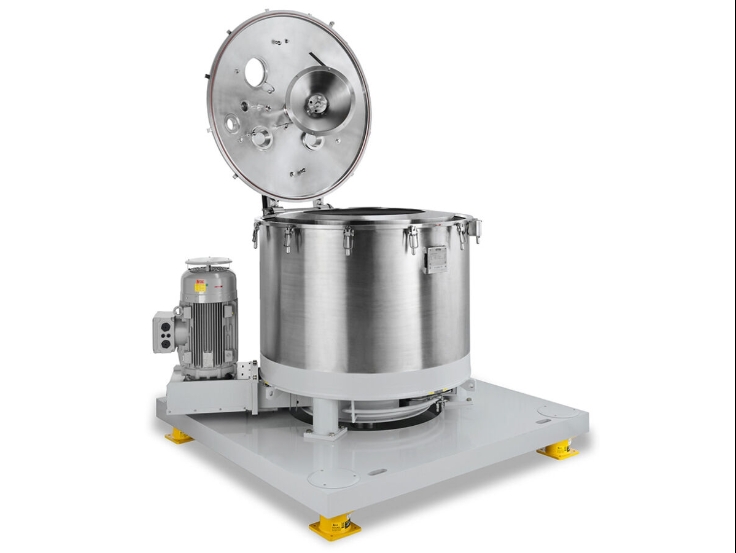
离心机与前后工序的匹配如何优化?
工艺流程总体规划
上游进料工序匹配要点
流量与浓度
温度与粘度
粒径与絮凝状态
物料缓冲与均质
离心机选型与工艺参数协调
设备型号与转鼓尺寸
转速与离心力
装料量与装料系数
运行周期与时序设计
下游工序对接与优化
滤饼处理(洗涤、干燥、造粒)
滤液回用或排放
包装与后续输送
自动化与联动控制
数据采集与监控
PLC/DCS 调度
反馈优化与在线调整
节能降耗与环保集成
热能回收
液体回用
设备运行工况优化
典型行业案例
制药中间体结晶分离
食品果汁澄清工艺
冶金矿浆脱水
验证与持续改进
试验小批验证
KPI 与 OEE 监控
改进闭环
结语
1. 引言
过滤离心机是众多行业中最常用的固液分离设备。其与上下游工序(如反应、混合、生化发酵、干燥、包装)环环相扣,稍有不匹配,就会导致产能瓶颈、能耗升高、产品质量下降或运行不稳定。通过系统化的工艺集成与参数协同,可实现“前进料顺畅、离心高效、后续处理平滑”,并最终达到生产效率与经济效益双提升。
2. 工艺流程总体规划
在开始具体匹配前,必须对整体流程进行总体规划,包括:
原料与产物性质:固含率、粒度分布、粘度、温度敏感性;
产能节拍:日产量、班次安排、连续/间歇模式;
设备布局与物流:进料泵、管网、缓冲罐、卸料系统;
质量与环保指标:CLARITY、残水率、洗涤液回用、排放标准;
自动化程度:数据采集、联动控制与过程优化。
3. 上游进料工序匹配要点
3.1 流量与浓度
流量平衡:进料泵流量与离心机处理能力应匹配,避免物料堆积或干扰离心平衡;
固含率控制:最佳固含率通常在10–30%,过高易堵塞、过低效率低;
缓冲罐容量:设计2–3倍单次进料量缓冲,兼顾间歇与连续模式。
3.2 温度与粘度
温度对粘度影响:温度升高可降低粘度,但可能影响热敏物料;
加热/冷却夹套:离心机配备夹套,可在进料前调整物料温度至最佳分离区间;
粘度检测:在线粘度仪监测,偏离时触发温调或稀释联动。
3.3 粒径与絮凝状态
粒度前处理:粗粒需筛分、细粒需絮凝或助滤剂添加;
絮凝剂投加:在进料缓冲罐中均质混合,保障滤饼结构与脱水性能;
在线比功能:浊度计或粒度分析仪可监测进料状态。
3.4 物料缓冲与均质
静态/动态混合:避免固体沉降或局部堵塞;
缓冲罐设定:配备搅拌与定量泵,实现平稳进料;
自动化调节:泵速根据离心机负荷自动调节,保持稳定液位。
4. 离心机选型与工艺参数协调
4.1 设备型号与转鼓尺寸
中小型机:间歇式,0.1–1 m³,适合批量工艺;
大型机:LWL 推料连续式,1–10 m³,适合高产能;
剖分设计:转鼓直径与宽度需与产能匹配,同时考虑场地限制。
4.2 转速与离心力
G 值设定:以分离难度决定,一般1000–3000×g;
软启动曲线:减少物料撞击,保护滤饼结构;
变频调速:工艺初段低速沉降、末段高转速脱液。
4.3 装料量与装料系数
装料系数 η:0.6–0.8(颗粒物)或0.4–0.6(胶体物);
装料量校准:结合鼓体体积 V 与物料密度 ρ,m=V⋅η⋅ρm = V·η·ρm=V⋅η⋅ρ;
在线称重:精确控制装料量,产能一致性。
4.4 运行周期与时序设计
间歇式周期:加料、分离、洗涤、脱液、卸料,常见3–5 min/段;
连续式时序:物料连续进出,卸料与加料同步进行;
全流程优化:使用SFC或PLC编排时序,减少空载时间。
5. 下游工序对接与优化
5.1 滤饼处理
洗涤段数:根据杂质浓度设1–3次洗涤;
吹气干燥:二段高转速+吹气脱湿;
卸料系统匹配:刮刀/推料/振动/翻转方式选型。
5.2 滤液回用或排放
回用:高纯滤液可回流至反应釜或洗涤;
监测:在线检测浊度、残油、COD,超阈则外排;
封闭管路:防挥发、抗腐蚀设计。
5.3 包装与后续输送
脱水后输送:皮带、真空吸料或螺旋输送;
成品特性:粉体需防潮,槽罐需真空或惰性;
自动化对口:与粉碎、造粒、包装线对接。
6. 自动化与联动控制
6.1 数据采集与监控
在线仪表:液位、压力、温度、振动、浊度;
数据平台:PLC→MES→云平台,实现实时报警与趋势分析。
6.2 反馈优化与自适应
根据实时浊度调整转速或离心时间;
根据装料量偏差自动调节加料泵;
智能化程序可实现批次自学习。
6.3 安全连锁
鼓盖、联动阀门、急停与物料泵联锁;
过载、过振、过热自动停机,联动报警。
7. 节能降耗与环保集成
7.1 热能回收
清洗水余热回收,循环利用;
冲洗用水预热至清洗温度。
7.2 液体回用
洗涤液循环在线过滤后复用;
滤液预处理浓缩后回原料库。
7.3 设备工况优化
变频节能,空载自动停车;
余压调节减少气源消耗;
自动化减少人为误操作带来浪费。
8. 典型行业案例
8.1 制药中间体结晶
原料含浊度高,需连续洗涤;
对接干燥段,滤饼含水率<20%;
实施智能控制联动,产能稳定提升15%。
8.2 食品果渣分离
滤液直接送罐装线,需高澄清度;
与包装线PLC互联,实时调节产量。
8.3 污水处理污泥脱水
连续推料式离心机,尾水回用;
配置节能变频与脱臭装置,全年节水50%。
9. 验证与持续改进
9.1 IQ/OQ/PQ 验证
安装确认参数对表;
运行确认产能与清晰度;
性能确认批次稳定性。
9.2 KPI 与 OEE 监控
产能达成率、离心时间偏差、滤饼含湿率 ;
故障停机时间、能耗指标 。
9.3 持续改进
定期评审装料-离心-卸料效率;
根据产线反馈优化程序与硬件。
10. 结语
过滤离心机与前后工序的匹配,是将单台设备性能最大化、保障产质量量与效率的关键。从上游进料——离心分离——下游处理——智能优化四大环节协同出发,结合理论+实验+数字化方法,能够真正构建高效、稳定、绿色的固液分离生产线。
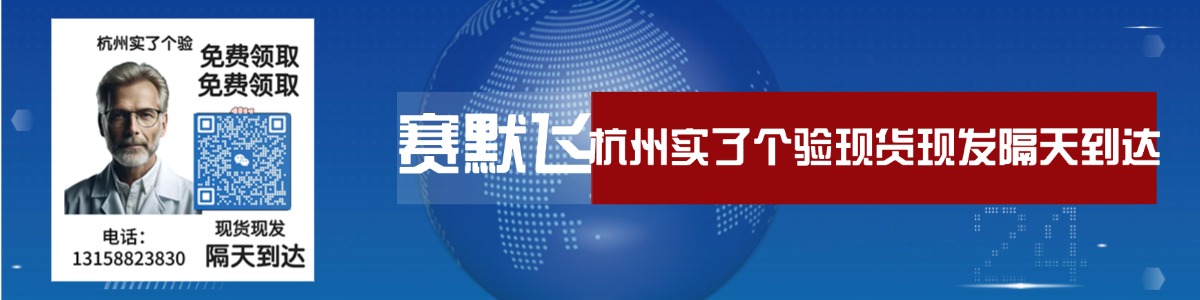