
电热培养箱可否集成到自动化实验系统?
一、什么是实验室自动化系统?
实验室自动化系统(Laboratory Automation System)是指通过控制技术、机器人平台、传感器网络、计算机集成、数据分析系统等多种手段,对实验室的样品处理、数据采集、设备操作、记录管理等环节进行自动化控制和联动管理。
典型的自动化系统包括以下部分:
硬件层面:
机械臂
移液机器人
自动化轨道输送系统
恒温设备(如培养箱、干燥箱)
光谱分析、质谱、离心、冷冻等辅助设备
软件层面:
控制软件(PLC、SCADA)
数据处理平台(LIMS、ELN)
远程控制与监控接口
云端存储与AI分析
通信层面:
以太网、RS-485、MODBUS、OPC等协议支持设备间通信与任务同步。
电热培养箱作为自动化流程中进行温度控制与样品孵育的关键节点,必须满足相关要求,才能与系统无缝融合。
二、电热培养箱集成到自动化系统的必要性
1. 提高实验效率
在传统人工操作中,样品放置、温度设定、时间控制均需人工完成,不仅效率低,而且易出错。将电热培养箱集成入自动系统后,可以根据实验流程自动触发温控操作、定时运行、数据记录等操作。
2. 实现多设备协同
在高通量筛选或多步骤实验流程中,培养箱往往与移液工作站、分液机器人、光学检测设备协同运行。只有打通数据与控制链路,才能实现流畅的样品传输与环境控制。
3. 满足数据完整性与可追溯性要求
制药、食品等行业对于实验数据记录与GMP合规性要求极高。电热培养箱若能与自动化系统同步记录温度曲线、运行日志、报警记录,将大大提升数据完整性。
三、电热培养箱集成自动化的关键要素
要实现电热培养箱与自动化系统的集成,需要满足以下几个条件:
1. 具备通信接口
电热培养箱必须内置通信模块,包括但不限于:
RS-232/RS-485接口:用于串口通信;
USB接口:配合驱动实现数据读取与写入;
以太网(LAN)接口:支持TCP/IP协议,接入局域网;
Wi-Fi模块:无线集成,适用于灵活布局;
IO端子:供PLC系统读取控制信号,如启动/停止、状态反馈等。
2. 开放通信协议或SDK
集成过程需了解设备通信协议,常见协议包括:
Modbus RTU/TCP:广泛用于工业控制,PLC系统易对接;
OPC UA/DA:适用于SCADA和工业软件平台;
厂商自定义协议:需要设备商提供开发文档、指令集、DLL文件或SDK。
3. 可程序化控制
设备须支持以下功能的远程触发:
温度设定
加热启停
时间参数设定
实时状态读取
报警信息获取
数据同步上传
4. 数据接口对接能力
与自动化系统的数据接口对接,实现:
实时温度数据流上传至中央数据库;
操作日志自动入库;
实验编号与数据绑定,实现样品-数据一体化管理。
四、电热培养箱集成的实现路径与典型架构
1. 集成架构示意
lua复制编辑 +---------------------+ | 实验室自动化主控系统 | | (PLC/SCADA/LIMS) | +---------------------+ | +-------------+-------------+ | | +--------v--------+ +--------v--------+ | 电热培养箱(智能型)| | 移液机器人/传送装置 | | RS485/Modbus/TCP | | 机械手、上位机等 | +------------------+ +------------------+
2. 实现步骤
选购具备通信能力的电热培养箱;
向厂商索要协议文档或SDK;
连接通信线缆/网络,测试设备连接;
通过自动化平台编程设定命令逻辑;
设置数据采集频率与变量映射;
测试系统流程并实施调试优化;
联动机械臂完成样品传递与培养操作。
五、实际应用案例分析
案例一:高通量微生物筛选平台
某生物科技公司构建高通量抗生素筛选系统,通过机械臂将样品移入带Modbus TCP通信功能的电热培养箱中,PLC控制系统控制培养时间并读取温度变化曲线,实验结束后自动将样品转移至分光检测仪,完成数据比对与记录。
案例二:制药企业GMP质量稳定性测试系统
制药厂对药品在不同温度下的稳定性进行长周期监测,电热培养箱通过OPC协议与实验数据管理系统集成,设定温度由上位系统控制,设备运行日志与报警信息实时同步至企业LIMS系统,满足GMP数据追溯要求。
案例三:智慧实验室统一管理平台
某高校构建智能实验室平台,使用基于以太网通信的智能培养箱,各设备接入同一管理主机。学生在Web平台设定实验条件,服务器将命令分发至各培养箱;实验结束后系统自动生成实验报告,包含运行日志、温度曲线等。
六、目前存在的技术瓶颈与挑战
尽管集成潜力巨大,实际应用中仍存在一些技术与管理障碍:
1. 设备标准化程度低
市场上电热培养箱种类繁多,接口标准与通信协议五花八门,难以统一集成管理。
2. 通信接口不稳定或不完整
部分设备虽标称支持RS-485或LAN,但接口功能有限,只支持监控,不支持控制。
3. 控制系统编程难度大
自动化系统集成需工程师具备PLC编程、电气调试、协议对接等多方面能力,非标准产品增加编程难度。
4. 安全机制不足
若未设置权限管理与安全认证,远程误操作可能导致实验失败甚至设备损坏。
七、未来发展趋势与优化建议
1. 设备厂商应标准化通信协议
支持开放式标准协议(如Modbus、OPC);
提供开发接口、说明文档与控制模板;
通过工业以太网实现统一接入。
2. 支持边缘计算与云端接入
培养箱内置微控制器或边缘网关;
本地控制+云端数据双保障;
实现远程调度、数据备份与AI分析。
3. 自动化平台向可视化、低代码发展
推出可视化流程编辑器;
降低非程序员操作门槛;
提供预设模块与参数模板。
4. 多维度安全控制设计
添加身份识别、权限控制、操作日志审计;
配置多级报警机制;
定期对通信进行加密升级与数据安全评估。
八、结语:从功能到系统的跨越
综上所述,**电热培养箱不仅可以被集成到自动化实验系统中,而且在当前智能实验室构建中扮演着重要角色。**这一集成过程不仅仅是设备功能的拓展,更是实验流程智能化、数据可追溯、管理集约化的必然趋势。
成功集成的关键在于选对设备、打通接口、配置软件、训练人员,并确保系统的可扩展性与长期稳定运行。随着工业物联网(IIoT)、智能制造、智慧实验室等概念的深入推进,电热培养箱正从一个孤立设备,演变为数据驱动型科研平台中的活跃成员。
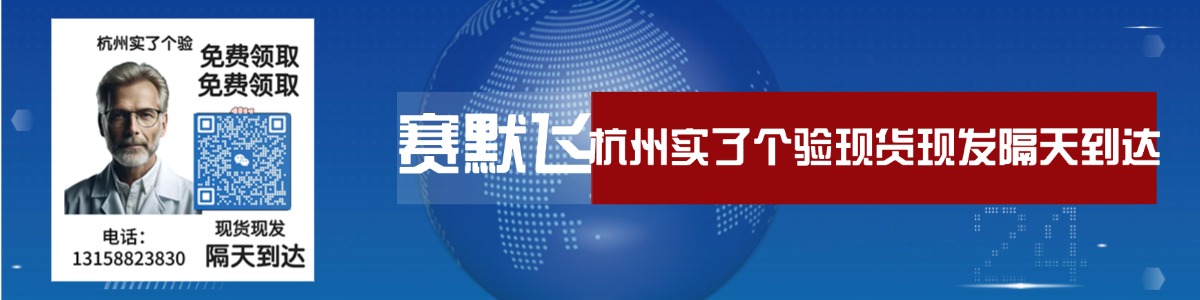